3D printen nu al in handbereik
Al lange tijd experimenteert Weber Beamix met 3D betonprinten. Al in 2005 verrees de eerste met betonmortel 3D geprinte muur laag voor laag. Het duurde nog tien jaar voordat de ontwikkeling op het gebied van 3D betonprinten in een stroomversnelling kwam door het 3DCP project van de Technische Universiteit Eindhoven. Binnen een consortium van bedrijven groeide dit experiment stap-voor-stap uit naar een nieuwe productiemethode in de bouw. Met als resultaat spraakmakende projecten en de opening van de eerste betonprintfabriek in Europa in 2019.
Tekst: Frank de Groot
Beeld: Weber Beamix
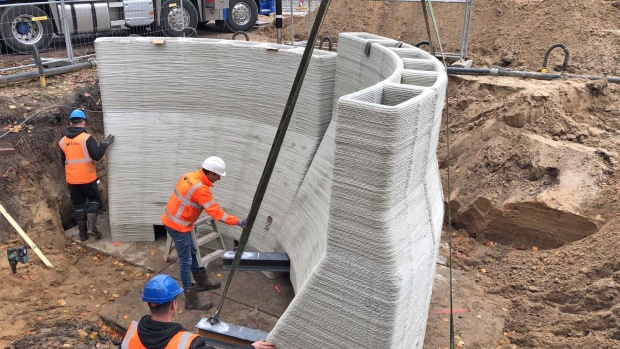
Plaatsing van de 3D geprinte keerwand van de uitstroombak in Zeist.
Op 15 januari 2019 opende Weber Beamix in Eindhoven Europa’s eerste commerciële, industriële productielocatie voor het 3D printen van betonnen elementen voor de bouw. Vandaag de dag is de productie in volle gang. Er worden diverse onderdelen geprint en in de praktijk toegepast. Er is zelfs een tweede vaste productiefaciliteit in Europa, een mobiele fabriek voor de verhuur en een vast productportfolio met onder andere op maat gemaakte taludtrappen.
Voordelen
Het printen van betonnen elementen voor de bouw heeft in een aantal situaties grote voordelen in vergelijking met klassieke productietechnieken:
- Natuurlijke vormen. Een ronde unieke geometrie kost ontzettend veel tijd om te bekisten. Met 3D printen los je dit op door de exacte vorm te printen. De prefab onderdelen zet je in elkaar op de bouw.
- Vermindering materiaal. Normaliter worden bekistingen compleet volgestort met beton. Een eerste uitgangspunt voor 3D beton printen is materiaalvermindering. Met minder materiaal hetzelfde resultaat behalen, betekent ook minder CO2-uitstoot. Daarnaast is er geen bekisting nodig, wat weer voordelig is met betrekking tot verbruiksmaterialen.
- Automatiseren van bouwwerkzaamheden. Door de unieke vormen als prefab onderdelen, genummerd aan te leveren op de bouw versnel je de bouw ontzettend. Het initiële ontwerp wordt exact gemaakt en daardoor heb je geen afwijkingen in de realisatie. Het gehele productieproces verloopt beter en sneller en de foutmarge neemt af.
Serie van 1
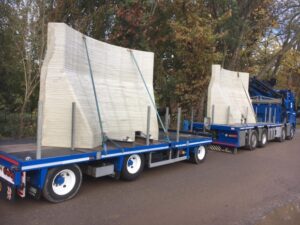
De geprinte elementen voor de uitstroombak op transport.
Volgens Pieter Bakker, Projectleider 3D printen bij Weber Beamix, wordt door 3D printen van betonmortel individuele seriematige productie mogelijk. Hierdoor ontstaat een enorme vergroting van de vrijheid in ontwerpen. Pieter: “Het toverwoord is slimmer bouwen, onder andere parametrisch ontwerpen. Dat is een proces waarbij modellen of ontwerpen automatisch worden gegenereerd op basis van parameters, zoals maten, materiaaldikte of geometrie. De printrobot kan eindeloos variëren op basis van verschillende parameters. Je kunt bijvoorbeeld alle kolommen van een brug of viaduct een verschillende vorm geven. Bovendien legt de printer alleen beton neer daar waar het nodig is voor de constructieve sterkte. We halen daardoor besparingen van 30 tot 40 procent. Ook is er geen bekisting meer nodig, dus is er ook geen afval meer.”
Verder verloopt volgens Pieter het gehele proces sneller en neemt de foutmarge af. Tijdens het ontwerpproces kijkt iedereen naar hetzelfde ontwerp. Wijzigingen worden direct digitaal doorgerekend en toegepast. “Je drukt aan het einde bij wijze van spreken op ‘Ctrl+P’ en de printer begint direct met de productie. Voor de bouwplaats is het belangrijkste dat er minder tijd op de bouwplaats nodig is, dus ook minder manuren. Dat betekent sneller, maar ook veiliger werken en de bouw wordt voor jongeren aantrekkelijker door automatisering en robotisering. Voordeel is verder dat je minder mensen op de bouwplaats nodig hebt, wat in deze tijd van schaarste aan vakmensen belangrijk is.”
Uitstroombak
Gevraagd naar een mooi project met 3D geprint beton noemt Pieter de uitstroombak bij het vernieuwde Station Driebergen-Zeist. Hier zijn in de buitenruimte verschillende elementen in de fabriek met een betonprinter gemaakt. Naast een viertal niervormige bomenbakken, variërend van 30 tot 80 meter lang, werd ook de keerwand van een uitstroombak met een 3D printer gemaakt.
Omdat het stationsplein erg laag ligt, wordt stuw- en hemelwater opgevangen in een ondergrondse bak met overloop. Zodra de bak vol is, wordt het water via de uitstroombak in een naburige zaksloot gepompt, zodat het water in het gebied blijft. De keerwand heeft een gebogen vorm en door de grondkerende functie verloopt de dikte van circa 1,20 meter aan de basis naar circa 0,50 meter bovenin. Stefan Bloemberg was toentertijd uitvoerder van BAM Infra op dit project: “Zo’n element is bijna niet te bekisten. Dus ook hier bood de 3D printer uitkomst. De kosten van de geprinte verloren bekisting waren gelijk aan die van het begrote traditioneel bekisten. Het grote voordeel zat hem echter in de grote besparing op arbeid en doorlooptijd.”
Pionieren
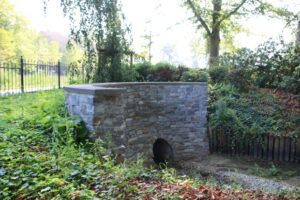
Eindresultaat halfronde keermuur van de uitstroombak.
Het project in Zeist was op veel vlakken nog pionieren voor de uitvoerende partijen. Stefan: “De 3D geprinte bloembakken en uitstroombak waren hol en zijn met transport en plaatsing dus fragiel. Bij de plaatsing van het eerste deel ontstond wat schade. Door het aanbrengen van verstevigingen aan de binnenzijde verliepen de volgende plaatsingen probleemloos. Verstevigingen zijn inmiddels niet meer nodig. Dat is nu eenmaal innovatie.”
Hij vervolgt: “Groot voordeel van deze werkmethode is dat het veel sneller gaat. Als je alleen al die uitstroombak had moeten uitkisten ben je drie weken bezig. Nu komt de ‘bekisting’ in één keer aan. Je kunt ook hele moeilijke vormen maken. Je bespaart dus enorm op arbeidskosten en je kunt maatvaster werken. Daarnaast werkten we toen met veel buitenlandse arbeiders die de Nederlandse taal niet machtig waren. Die vakmensen kun je niet ineens een complexe bekisting laten maken. Maar ze kunnen de bakken wel plaatsen en na een goede uitleg kunnen ze ook de naden tussen de delen zelf afstorten. Daartoe werden er bekistingsplaten tegen de naden geplaatst en vervolgens werden die naden gevuld.”
Toekomst
3D printen heeft volgens Stefan in ieder geval de toekomst. “Ik werk nu bij defensie als opleider en hier werken we ook met 3D printers, maar dan voor kunststof en rubber. Zo kunnen we zelfs modulaire wapenaccessoires printen! We hebben een printer waar aan de ene zijde kunststof PET-flessen in gaan en aan de andere zijde een 3D geprint product uitkomt.” Pieter Bakker besluit: “Ik ben er van overtuigd dat 3D betonprinten zijn plek in de markt aan het opeisen is. De techniek staat niet meer in de kinderschoenen, maar we hebben ook echt nog wel voldoende uitdagingen voor ons.”
Weber Beamix
www.nl.weber